Taking a proactive approach to routine, scheduled packaging audits can improve the quality of your packaging and keep your specs compliant, which in turn, can minimize product recalls due to faulty packaging or improper labels. We’ll look at 3 specific ways that audits can help.
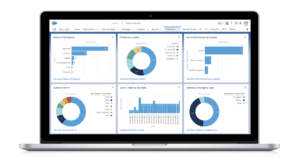
1. Using audits to improve quality
Packaging specifications are constantly changing as new techniques are developed or as company marketing teams initiate new brand campaigns. Making sure your suppliers receive and implement your packaging changes can increase the quality of your packaging and reduce non-conformities.
By creating packaging audit procedures and checkpoints based on business rules your company can ensure suppliers are meeting your quality standards. An audit every 6-12 months should suffice, however, when new packaging is introduced, new products are launched or changes are made to packaging, it is wise to implement a supplier audit within 1 month of the launch/change. A repeat audit at 3 months is advised to ensure consistency of the packaging specs over time. If the first two audits show no non-conformities, a 6-12 month audit cycle can be implemented.
2. Using audits to determine root cause
Major retail chains have strict packaging requirements on goods producers and failure to meet them can have detrimental results. One packaging failure can make the difference between continuing to be an approved supplier and loosing the entire account. Imagine your company supplies a large retailer with product. During the delivery of a shipment, the packaging fails to the point the retailer no longer desires to carry your product. For some goods producers, this scenario can be disastrous.If this unfortunate event should happen, performing an audit on the failed packaging against your approved specifications can help to determine root cause and provide valuable data for potential lost revenue claims. By requesting an audit of the supplier, it can be determined if the specs themselves were faulty or if the packaging supplier did not provide packaging according to the specs. If this is the case, your company will have a claim against the packaging supplier for lost revenues.
3. Using audits to minimize returns/recalls
Product recalls, particularly food recalls due to improper allergen labeling is on the rise and can be costly for even established, successful companies. The best method for reducing the risk for returns and recalls is to develop a pro-active review and audit process for product packaging and labeling.
Here are the top three reasons for packaging/label failures
- Packages for similar products made with different allergens, or products with and without allergens packaged in similar packaging.
- The wrong terminology in the ingredient list or the allergen “contains” statement.
- Changes in formulation/ingredients from external suppliers not carried over to the final product label.
Auditing your suppliers to ensure compliance with label designs/regulations helps to keep your specs compliant and confirm your label matches the certified spec, ensuring accuracy and minimizing returns and recalls.
If your company is using outdated technology like PDF files, spreadsheets or inflexible ERP solutions to manage your packaging/labeling specs, consider Specright, the Intelligent Specification Management Platform. Our customers use Specright’s Exchange to share accurate, approved specs with suppliers real-time, reducing their risks for recalls due to improper packaging/labels. Plus, our packaging Engineering Services team can perform audits of your packaging on a regular basis.