In my role as a marketing leader, I get to spend time out in the field talking with customers across industries and functions. I always ask the same question: what is keeping you up at night?
Lately, there has been a resounding theme: the coronavirus is wreaking havoc on global supply chains and it’s keeping supply chain leaders up at night. In addition to the serious impact of the coronavirus outbreak on people and communities, the results of containment strategies - self quarantines, travel restrictions, and other public health measures - are bringing supply chains to a stand still.
How Does the Coronavirus Impact Supply Chains?
So how does this growing pandemic impact supply chains?
First, it disrupts major manufacturing centers.
As part of increasing globalization, China has emerged as a key manufacturer for many companies around the world. Plants across the country have slowed to a halt as a result of workers needing to self quarantine to contain the spread of the virus. Companies in the US and elsewhere that rely on these manufacturing facilities are now trying to fill demand elsewhere, and many don’t know where to easily turn.
In addition to manufacturing, the country is also a key link in the supply chain as a source of raw materials. The workforce challenges and logistics limitations are preventing raw material supply from moving around the world to other manufacturing facilities. So even if supply chain leaders have capacity in other facilities, they still may not be able to get the raw materials to make their products.
While the interconnectivity of global supply chains has led to tremendous leaps in production, it has also created an extremely fragile chain that can be disrupted if a single link is out of place. So how can supply chain leaders address the immediate challenges of moving supply chains? It all starts by managing specifications and the critical data to make a product, ranging from supplier tiers and contingency plans, to machine line and equipment requirements.
The Challenges of Moving Supply Chains
After speaking with a global procurement executive, I recently learned about a standard contract clause in supplier agreements called “Force Majeure,” which is french for “superior force.” According to Contracts and Standards, the definition is, “a contract provision that allows a party to suspend or terminate the performance of its obligations when certain circumstances beyond their control arise, making performance inadvisable, commercially impracticable, illegal, or impossible.”
The Coronavirus is certainly a force majeure - and while many procurement professionals are able to sever ties with suppliers, it doesn’t mean they can quickly find a solution or replacement. At Specright, our Specification Data Management™ platform is helping leaders and operators better understand their supply chains - and quickly surface different options when disruptions arise - so companies can quickly take action.
Here are three ways supply chain leaders can use Specright to identify and mitigate the risks of the coronavirus outbreak. And for companies not on the Specright platform, we’ll talk about how Specification Data Management can help with the next “force majeure.”
3 Steps to Move Your Supply Chain with Specright
1. Quickly Pinpoint Suppliers at Risk
The first step is being able to quickly understand what suppliers are at risk.
Believe it or not, many professionals don’t have Google maps for their suppliers. In Specright, we’ve built just that - and our customers are able to quickly put in a location and radius to see what suppliers are potentially impacted. This is helpful not just for global health concerns, but also being able to triangulate weather events like hurricanes in the Gulf to see what supply or suppliers are potentially impacted. Having a head start on information like this can help procurement and other supply chain professionals more quickly put together contingency plans.
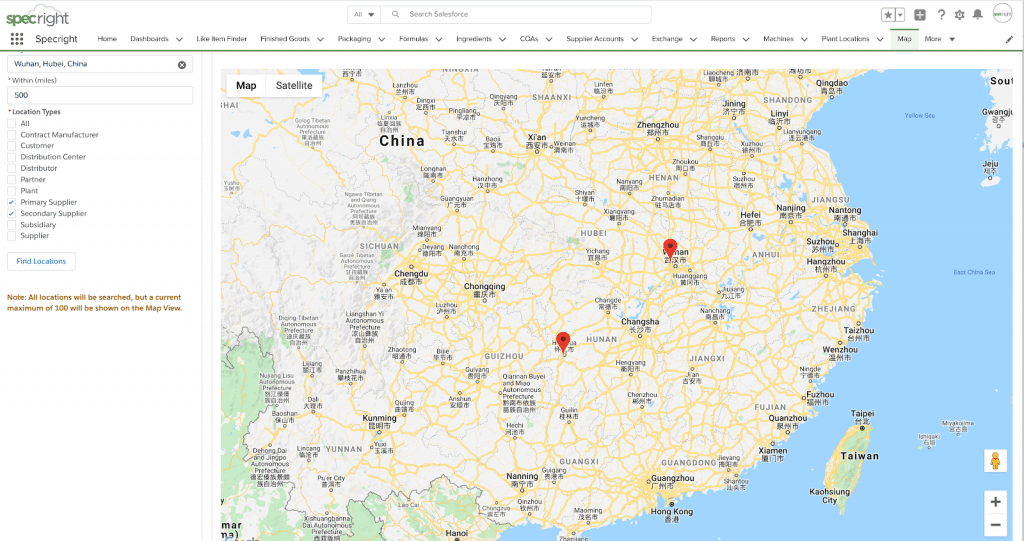
2. Understand What Products or Materials are Impacted - to the Specification Level
Once you’ve identified the supplier potentially impacted by the supply chain event, you need to understand what they’re producing down to the specification level. A specification is the DNA-level data it takes to make a product or packaging and includes things like ingredients, formulas, raw materials - even down to what machinery lines produce it or pricing modules for how you buy it.
With Specright, you can quickly click into the supplier and immediately see the exact specifications and finished goods they’re producing. When I talk to customers, this is one of the biggest challenges I see - many of them previously relied on suppliers to manage specifications on their behalf. Not having this data firsthand prevents supply chain teams from being able to quickly go to bid with new suppliers or share the specification currently in production with other suppliers or manufacturing facilities in a time of crisis.
By centrally managing digital, live specifications, supply chain leaders can make their supply chains more agile and flexible and move quickly in a time of crisis. Which leads us to our final step.
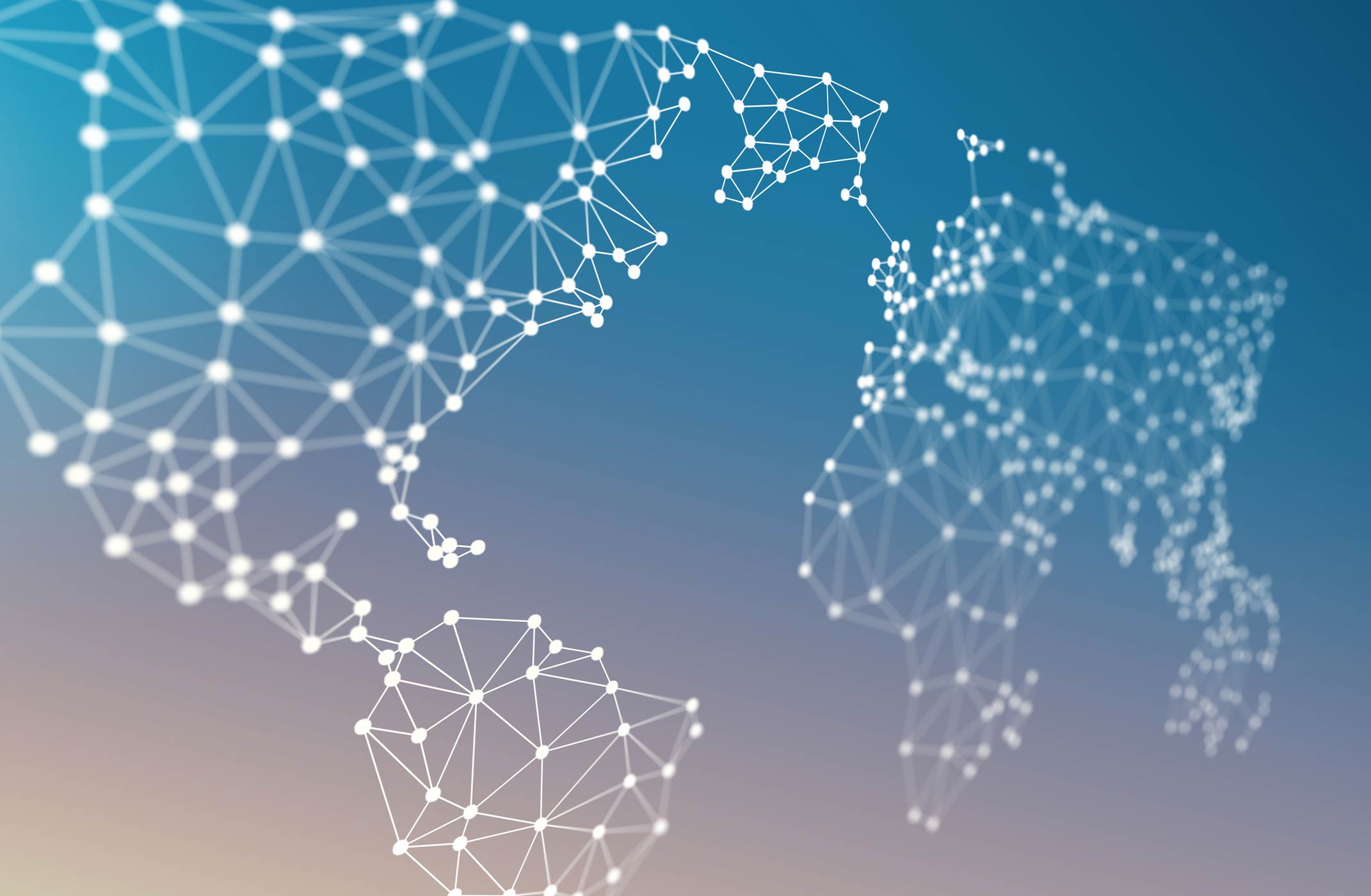
3. Identify Other Facilities or Suppliers to Fill the Supply
Once you’ve identified the impacted suppliers and the specifications of products impacted, you need to quickly identify where you can shift supply or manufacturing.
One customer told me she’s in the middle of doing exactly that, with one problem: the lines in each manufacturing facility are different. As a result, even if she has identified alternate suppliers or facilities, they may not be able to quickly get production up and running.
With Specright, our customers are mapping the specifications of their machinery lines so they can quickly understand what products could be produced where. Understanding the compatibility of products and manufacturing facilities can prevent costly slowdowns by flagging problems before they happen in production.
In terms of finding alternate suppliers, many procurement teams have well-established tiers of primary, secondary and tertiary suppliers. However, finding all the relevant supplier information, contracts, and easily sharing specifications can be a challenge. In Specright, users can easily segment suppliers by tier, access terms, and quickly share specifications to get up and running.
In Conclusion
There are certainly more important things to worry about now than the state of supply chains. But the reality is many of our customers are providing products - ranging from bottled water to sanitizing wipes - that people are relying on to stay safe. By arming companies with specifications and the data they need to manage their supply chains, we hope to help companies mitigate the impact of supply chain challenges so people can get the products they need in a time of crisis.
In this webinar, you'll learn how to mitigate the impact of supply chain disruption through Specification Data Management.
By centrally managing specifications, you can easily identify alternate suppliers and move specifications, visualize the impact of natural disasters on your supply chain and quickly get production back up and running.