Product lifecycle management (PLM) is integral for businesses that manufacture products. This comprehensive guide will explore what PLM is, the benefits of PLM, and the future of PLM technology. PLM, a business discipline, facilitates product data management (PDM) in every stage of a product's existence. From when a product developer conceptualizes a product to its service and disposal, a product will have many details that must be managed efficiently.
Today's circular economies and transparent supply chains necessitate a product's management throughout its lifecycle, starting with the raw materials used and ending with recycling or repurposing. This helps manufacturers create a successful PLM strategy that enables them not just to integrate but also to make meaningful innovations when the time calls for it.
This comprehensive guide will explore PLM in detail, looking into how managing products throughout their lifecycle using a robust PLM software system streamlines processes for organizations and what challenges it presents. It will also spotlight what the PLM technology holds for organizations' future, giving us an overview of its future capabilities and how they will enhance the operational efficiency and productivity of manufacturing professionals.
What is Product Lifecycle Management (PLM)?
Product lifecycle management (PLM) is a strategic approach to meticulously oversee and manage products throughout their lifecycle. This approach involves coordinating all aspects of a product from conception to disposal, ensuring efficiency and effectiveness in product management - similar to Packaging Management Software Solutions, It starts with the conceptualization stage and ends with disposal. When effective product lifecycle management is implemented, it brings together employees from different departments who work collaboratively to bring products to life. Managing product details, including raw materials used, in a central location enables everyone, from the product designer to the product engineer, to access the most up-to-date information, reducing data errors and maximizing productivity.
PLM serves as a potent tool for designers, engineers, marketers, and others to create, manage, and optimize products effectively, enabling them to maximize their profits. A PLM strategy is more effective when complemented by a solid enterprise resource planning (ERP) system. With ERP modules like inventory and supply chain management, vital product data is centralized. This helps connect all aspects of a product’s lifecycle to minimize repetitive and labor-intensive work and provide real-time and accurate data access.
What is PLM Software?
PLM software is a digital solution that helps organizations manage all data regarding products to efficiently carry out processes at every stage of product development and lifecycle across globalized supply chains. This software supports both new product development and the upgrading of existing products, facilitating efficient and sustainable market launches. Product data typically includes information about items, parts, products, requirements, engineering data, bill of materials (BOM), and workflow data.
In the current manufacturing landscape, a significant trend is adopting software services, such as product-as-a-service (PaaS), which helps companies introduce new products and services to their markets. As a result, many organizations feel the need to use cloud-based PLM software that helps them stay responsive and agile. Modern PLM software tools have thus emerged as a crucial component in business transformation, as they offer the digital enterprise product record deemed essential for revolutionizing product development and supply chain strategy.
How does a PLM system work?
A PLM system is designed to offer product designers and engineers real-time access to crucial product data. It streamlines project management by connecting CAD (computer-aided design) data with bills of materials and other enterprise data sources, including integration with an ERP system. This system centrally stores and manages all product data for a product's development and lifecycle.
PLM is also instrumental in breaking down data silos, helping designers and engineers gain insights into external sources, such as customer needs and analyst feedback on current products, products' on-field performance data, and downstream business processes like manufacturing.
Beyond providing up-to-date product information to design and engineering teams, a PLM system guides other teams by providing a single source of truth, enabling suppliers and business stakeholders to make critical decisions quickly based on feedback. Incorporating PLM technology into your daily processes means a unified product value chain will facilitate business planning and supply chain activities to drive innovations and release improved products to market more quickly.
Why Do Companies Need PLM?
Businesses face growing complexity in areas such as product design, supply chain management, distribution, and customer feedback. At the same time, global competition adds to the complexity by driving prices down and causing regulations to shift. To tackle this effectively, businesses need a PLM solution that can empower them to create high-quality products and bring them to market faster to keep making profits.
With an effective product lifecycle management strategy that includes PLM software, companies can carefully monitor and analyze each stage in a product's lifecycle and track its relationship with other stages to efficiently manage all aspects of the product lifecycle. PLM ensures knowledge is captured and stored well, facilitating easy access to information and teamwork.
Benefits of Product Lifecycle Management
PLM does more than create a direct link between information integrity and an organization's effectiveness in tackling product requirements. Here are five ways in which PLM software can help organizations step up their game:
Improvements to development, engineering efficiency, and effectiveness
Studies have suggested that data silos are the biggest reason why the engineering team's performance suffers. PLM effectively eliminates these silos and allows the bi-directional flow of real-time product data to support better knowledge-sharing and collaboration between different teams across departments.
Elimination of errors during the engineering release process
Once a product is ready to be released to the market or has already been released, any defects or issues identified can result in costly fixes or recalls. Identifying product issues early on and fixing them before the product enters the market is much easier and cheaper. PLM simplifies problem detection and helps organizations trim unnecessary costs while offering the added benefit of reducing environmental waste.
Reduced time to market
PLM gives project managers the ability to prevent overlapping timelines and get products to market faster by providing them with a single source of truth with up-to-the-minute product data at every step of the product lifecycle.
Improved project delivery
A company-wide PLM software solution can help introduce and support advanced workflow management. PLM enables teams to effectively manage the handover to manufacturing new designs by precisely calculating product costs.
Higher quality designs
PLM assists designers and engineers in getting a deeper level of insight into product requirements by deriving data from different internal and external sources, enhancing visualization capabilities. With its integrated machine learning, a PLM can convert performance data and customer feedback into new feature suggestions.
Overcoming PLM challenges
Many organizations face issues when it comes to developing complex products. They need to deal with different systems, processes, and departments that operate disconnected from each other. They also struggle with poor data quality and frequent changes in engineering orders, which result in inaccuracies and increased costs. Additionally, many R&D executives are concerned about not fully understanding the entire product development process due to a lack of a single source of product truth.
To overcome these challenges, the adoption of a robust data sharing PLM system is necessary to streamline product lifecycle management. However, the investment may only be fruitful if the data is captured, analyzed, stored, and shared safely. This highlights the need for an ERP system with integrated AI, machine learning, and data encryption capabilities so that it offers an end-to-end value-based solution for everyone across the organization and not just for product engineers.
Future of PLM technology
Staying ahead of competitors, attracting top talent, and producing high-quality, sustainable products is getting more challenging. PLM can meet these challenges by enabling conscientious design and engineering, but only if organizations invest in the required technology.
With more things increasingly becoming interconnected via the Internet of Things (IoT), designers and engineers stand to benefit by gaining better insights into products being used in the field or by consumers. Explore further by viewing our webinar on navigating AI, building trust, and driving innovation to see how advanced technologies are integrated into PLM systems.
Sustainability is gaining importance every single day, and leading businesses seek to modernize product development for greener design, manufacturing, and logistics. PLM bodes well for manufacturing units across companies as it can help support a fully sustainable supply chain.
PLM systems are now hosted using cloud services such as Software as a Service (SaaS). This directly translates to more companies using them to support collaboration between employees distributed across locations.
Digital twins, virtual models connected to their physical counterparts via IoT within PLM systems, are an emerging concept and expected to contribute substantial cost savings for manufacturers. According to IDC, 65% of global manufacturers have achieved 10% savings in operational expenses only by using digital twins. Gain further insights into this digital shift by watching our webinar focused on reimagining supply chain with a spec-first approach, which covers the essentials of digital transformation in PLM.
The Difference between Product Lifecycle Management and Specification Data Management™?
Specification Data Management (SDM™) and Product Lifecycle Management (PLM) share similarities, but the two terms are far from interchangeable.
By definition, PLM software is a repository of data used in the design and manufacturing process of a product throughout its lifecycle — development, rollout, growth, stability, and decline. The idea behind using PLM software is to facilitate both the manufacturing and marketing aspects of a product to inform decision-making.
The functionality, purpose, and the resulting impact on the supply chain and workflow affect business operations in different ways. Let’s do a side-by-side comparison to uncover the most important differences between SDM and PLM.
Foundational Purposes
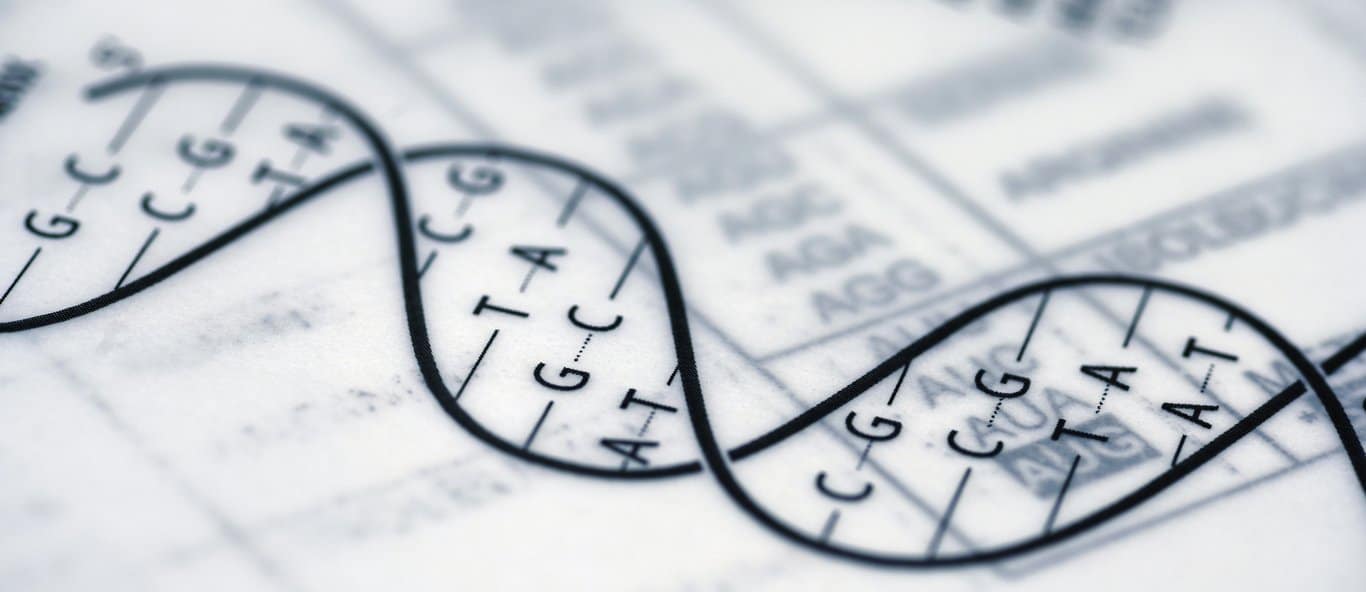
SDM takes a unique approach to product development and management.
When scientists first discovered they could sequence the human genome, the revelation had a huge impact on the medical world. Now, instead of treating the symptoms of a disease, scientists are able to discover and treat the root cause of an illness.
We compare SDM to this medical milestone.
SDM allows companies to dial in on their product-related data at the spec level and fundamentally change how they do business, allowing rapid iterations and improvements.. From the way you track quality to how and where you source materials, SDM enables companies to move further upstream and identify issues before they become problems. SDM isn’t a solution that is marginally better than what companies are using today, but rather a completely different approach and purpose to product development and management.
For comparison, while PLM has a much longer tenure in the industry, it serves a different purpose: to manage a product’s lifecycle at the surface level. Companies can see at a glance where products are in the development stage, how they’re being produced, how they’re being marketed, and whether they’re selling, giving companies data-driven insights they can use to make key business decisions.
However, PLM lacks the finer level of detail that SDM provides to help gain even deeper development, production, service, promotion, and sales insights into each product.
The Intended User
PLM was originally developed to be used by engineers on-site to design and collaborate on products in development. That said, the benefits of PLM are limited.
In the past, PLM technology was on-premise, so it was only used by internal employees. Today’s PLM has moved into the cloud and is now leveraged by other organizational roles, including sales, marketing, and customer service. However, PLM still maintains the original structure and functionality that was made with the engineer in mind. The complexity of PLM software’s interface and features aren’t designed for other users who would benefit from the data it contains. This leads to potential collaborative barriers and delays in the product development journey.
By contrast, SDM was designed to be shared across the organization and with external partners through an intuitive interface, accessible across computers, tablets, and mobile devices. It can also integrate with other enterprise systems, such as ERPs. SDM was designed as a cloud-based platform and caters to roles inside and outside of the organization, including vendors and suppliers, engineers, designers, sales and marketing teams, product quality assurance, procurement, and art departments.
All of these supply chain functions need to access product and packaging specifications to bring a product to market. The fact that many of these organizations operate in siloed systems today results in losses, inefficiencies - even product recalls. Even companies with multiple locations - domestic and international - can tap into a single source of truth with no loss of information or productivity.
Product-Focused vs. Process-Focused
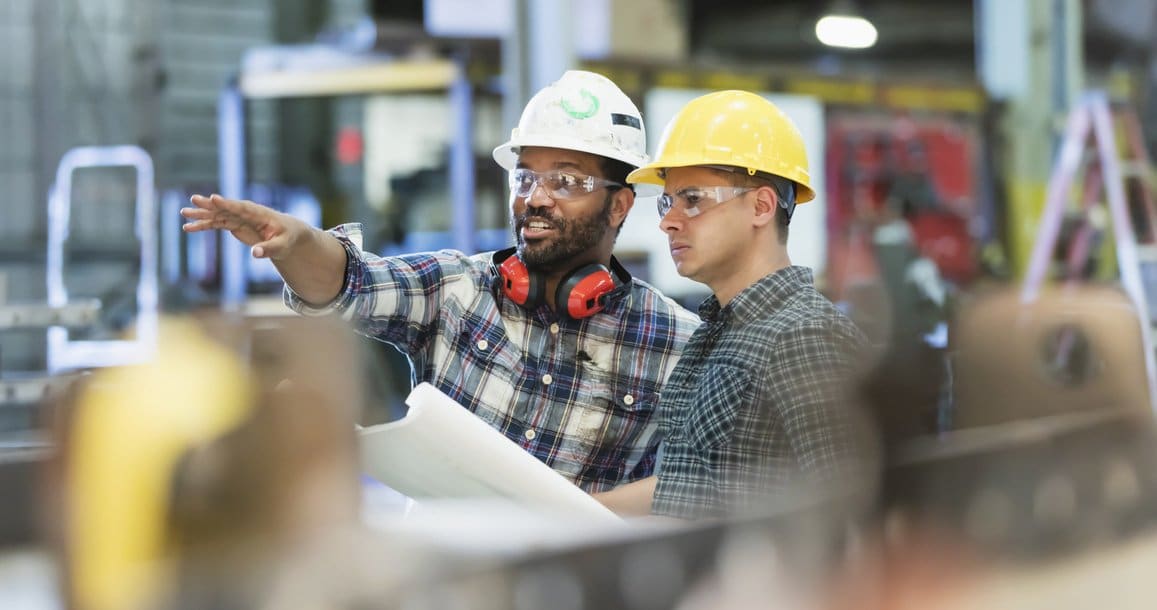
When product details are managed correctly, other systems become more efficient.
For instance, as product development progresses through stages, it becomes more and more difficult to implement engineering changes. Although today we have computer-aided design tools to reduce the scope of errors, these tools do not operate on their own. They still require time and resources that can derail your project from predefined deadlines.
Now, when you have a perfect product design from the get-go, the subsequent steps, like manufacturing, distribution, and marketing will be a breeze.
As the name implies, Product Lifecycle Management focuses on the product's journey throughout its life. From the early stages of development until the product reaches its end of life and leaves the market, PLM helps companies optimize the production process, streamline their time to market, eliminate bottlenecks, and reduce errors and waste.
SDM can offer these advantages, but with a more granular approach that enables more robust business outcomes and decision-making. Rather than look at the product as a whole, SDM focuses on the individual specs and the processes associated with each.
Let’s say you have a new snack product. Your PLM will help you create all the parts of the product (in this case, the packaging and the snack itself), create a prototype, plan the production process, deliver the product, monitor its success, manage the product launch, and remove the product from the market when the time comes.
Now, let’s say you’re also using Specification Data Management software to create your new snack product. SDM will digitize each element that goes into the product, such as the raw materials, ingredients, and manufacturing line components. SDM will create a map of these specs to create relationships, such as combining ingredients to create a formula that will become the finished good.
SDM goes into finer details of the product portfolio and also factors in budgets, quality management, production costs, and other metrics to give you a holistic view of the process so you can manufacture quality products that dominate the market.
With these elements in place, you can take it a step further to see how each of your components affects each other and your company as a whole. Here’s one of the use cases: you might test a change in suppliers in your SDM platform to see how the switch might impact your profitability.
Product ideation takes a lot of time and resources. Therefore, it’s important to avoid recurrent costs associated with ideation and other processes that take place prior to product development. That said, one of the greatest benefits of using a specification-first rather than process-first approach is that you don’t have to reinvent the wheel when you want to create a new product, promoting the reuse of existing components. You can simply clone and tweak an existing product and immediately know where to get all of the product’s inputs. Once you lay out the product’s DNA, you can intelligently execute your new product and maximize your profitability, sustainability, innovation, and operations.
Usability and Flexibility
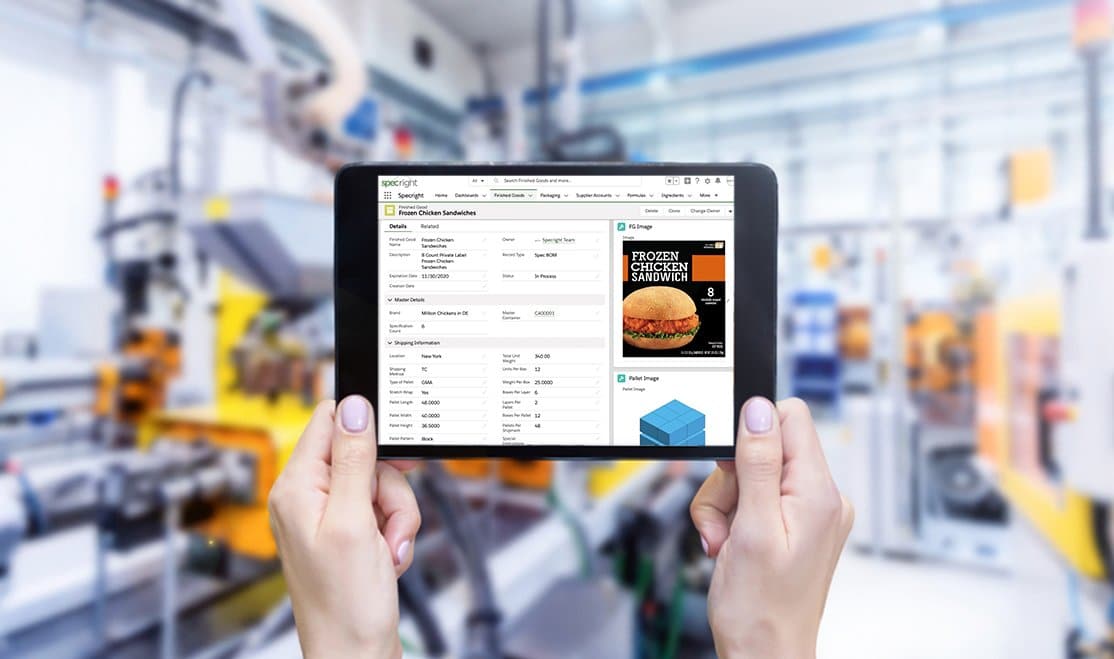
PLM is designed to be product-specific, which limits its scope considerably. Lacking the agility to provide actionable insights right off the shelf, PLM is highly customized. This means that, from a process perspective, leveraging PLM technology involves a custom process for each product.
By contrast, SDM is much more flexible, allowing organizations to gain quick insights almost immediately upon implementation and streamline repeatable processes for quick product development or improvement to existing products. This more agile approach results in savings in both time and money, enabling organizations to bring new products to market more efficiently.
Thanks to its flexibility, SDM can be integrated with your existing PLM process in case you don’t want to replace the latter.
Can SDM Replace PLM?
SDM Enables the Needs of 21st Century Manufacturing, while PLM represents how things have been done in the past
One of the biggest questions we receive at Specright is whether Specification Data Management software is designed to be a replacement for Product Lifecycle Management software. While both systems aim to streamline processes, save money and resources, and allow you to make data-driven decisions for your business, SDM is designed to meet the challenges of manufacturing today.
In fact, many challenger brands that choose Specright never need a PLM, while some of our enterprise customers choose to have them integrated. When companies choose to use both SDM and PLM systems, their PLMs are improved because of the integrity of managing product DNA using a Specification Data Management as a data workbench.
There is not a one-size-fits-all approach: it depends on each company's needs, business goals, and challenges. We find that SDM also supplements and strengthens other systems, like Inventory Management Systems or Enterprise Resource Planning (ERPs), by tying inventory levels or purchasing levels to specifications or finished goods. This can enable outcomes such as better supply chain forecasting and demand planning.
When all of the fine details are accurate and accessible, every other process and system automatically becomes more efficient. The two systems accomplish different goals, cater to different users, and focus on different objectives. To learn more about why Specification Data Management is the future of the supply chain, download our ebook.