Specifications haven’t gotten the attention they deserve. While there are a lot of data management systems out there, only a few can really manage your specifications.
Today, most professionals are resorting to unconventional spec management systems, such as email, PDFs, over-configured ERP systems, and in spreadsheets like Excel.
While spreadsheets are great for a lot of things, managing specs isn’t one of them. After all, specs are a living piece of data; they change often, they’re shared often, and are vital to successful supply chain activity.
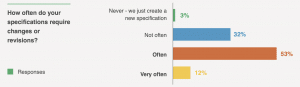
So the question is: why do so many professionals manage dynamic data in a static system?After all, you wouldn’t drive a self-driving car that could only stop or start automatically. You’d want one with the data infrastructure and intelligence to change courses easily, slow down or speed up, and proactively prevent accidents. Surprisingly, the data infrastructure required for specification management isn’t so different. But nevertheless, spreadsheets have persisted. And in times like the COVID-19 pandemic, we’ve seen how rigid and retroactive systems like Excel can lead to a lack of visibility when it comes to specification management. That’s why it’s time to stop using Excel to manage your specs - here’s our top 3 reasons why.
1. You’re Using a Long List of Solutions, Making Productivity & Collaboration Impossible
Rarely does a company only use Excel to manage specs. Why? Because Excel doesn't have the ability to efficiently manage processes like packaging, product development, procurement, quality, and more.Companies taking an Excel-approach to spec management typically have a long list of software solutions they use, that may or may not have the ability to communicate and share data. And without an easy way to share data, we see a lot of companies simply emailing files back and forth. Email might work on a small scale, but the majority of companies are managing more than 1,000 specs - and we’ve all missed an email at one time or another. Also, so much of the value in data is attributed to timeliness. Missing emails with Excel files of spec data can result in incorrect products being produced. Especially for industries like food and beverage or pharma, goods are perishable – Excel just doesn’t provide the instant and accurate communication supply chains need.
2. You Don’t Have Supply Chain Visibility, Turning Decision Making Into a Guessing Game
Without supply chain visibility, it can feel like different departments aren’t even a part of the same company. For example, before Specright, one of our customers shared that, “Everyone [in our company] had a different version of a formula.” This is because files were shared, downloaded to personal drives. When updates were made, it became difficult to ensure changes were communicated to different departments, suppliers, and co-manufacturers. And more often than not, when companies find themselves in a time crunch without the data they need, expensive decisions are made based on guesswork. This results in a slew of issues, such as product defects, damage during shipping, and poor product quality. And not only is data siloed, but problems are siloed, meaning other departments don’t know that there’s an issue until it’s way too late.
3. You’ve Got Waste Left, Right, & Center
We live in a world where there’s no time (or product) to waste. Between skyrocketing demand, product shortages, and delivery expectations, we can no longer afford to waste time and resources. We need systems that are easy to use and accurate.
According to Lean Six Sigma principles, there’s 7 types of waste: Inventory, motion, over-processing, overproduction, waiting, transport, and defects.Let’s take a look at just one of these as an example: over-processing.
Over-processing happens when employees are using unnecessary/incorrect processes or the wrong tool for the job at hand. This happens all the time, especially in industries where tribal knowledge is rampant. Imagine you’re a factory worker in a glass jar manufacturing plant. You’ve been in this job for 20 years, and have learned over time that you get the best results when you pull product out of the furnace when the glass turns a specific shade of orange, a slightly different amount of time than is listed on your SOP, but recognizable to a trained eye. How do you capture that data in a platform that communicates your findings in a shareable manner and can be found amongst the high volume of data surrounding manufacturing? Now imagine the way you manage your specs (machinery, processes, product, and all) is in Excel.
The issue with managing tribal knowledge in Excel is not only the limited data format, but also capturing change history and being able to keep track of data for a long period of time.Without a way to capture that data, future employees end up with product damage or defects, overproduction to replace those products, and slower speed to market, all amounting to massive levels of waste.
If Not Excel, Then What?
Specright is the first purpose-built platform for Specification Management and a fundamentally different approach to bringing products to market by starting with DNA-level specification data. Instead of spreadsheets, Specright creates digital, cloud-base specs that can be easily viewed and shared. Whether it’s packaging, raw materials, formulas, products, or machinery specifications, there are thousands of data points and processes at companies today that are held as tribal knowledge or in silos causing unknown waste. With Specright, companies can centrally document, map and manage their information, transitioning it from spreadsheets to a secure online Specification Management platform that can be used by the next generation of professionals entering the workforce.
With Specright, spend less time on email ,and more time doing what you were hired to do. For more information on how Specright can help you, reach out to a member of our team.