Over the past few weeks, companies across the country have struggled to find ways to enable remote work while continuing day-to-day business operations as the COVID-19 outbreak, commonly known as the Coronavirus, has created unprecedented challenges in all areas of our personal and business lives. In an attempt to limit the spread of the disease, many companies are transitioning their employees to remote work and encouraging social distancing.
Practically speaking, it’s not as simple for manufacturing organizations to follow this course of action.
Enabling Remote Work in Manufacturing
Although it’s impossible to transition the people physically working in plants to home-based operations, manufacturing companies can enable more headquarters and non-essential plant employees to work remotely while keeping a pulse on the business. This is especially important in terms of supply chain management as we’ve learned through recent product shortages.
Over the past few weeks, many of my customers have reached out to me and my team to share stories of how Specright has enabled them to work remotely. They’ve shared how using a Specification Data Management™ platform has helped them map and understand their supply chains so they’re better informed in situations like this. When manufacturers transition their data to a cloud-based platform, the ability to enable remote work becomes much easier.
Before Specright, many of them were leveraging PDFs or excel files to manage specifications and related data such as quality, supplier and procurement information. Or they had to physically be in a company building to leverage a home-grown system or attempt to log into a VPN to connect to an outdated database with onsite servers. In plants, passing product, samples, and data back and forth still requires hand-to-hand interaction.
"Even in cases where systems were accessible, the speed and performance of them would not meet our expectations, nor the need for rapid response in this moment."
With Specright, remote workers can use their phones, tablets, or computers to log in and within seconds have access to everything they need. They can still log quality issues, create new specifications, or find suppliers from the comfort of their home. When I think back to my time running manufacturing facilities, it would have been unthinkable to engage with my customers during this time or enable this kind of remote work without Specright.
There isn’t a one-size-fits-all approach, but it’s my commitment that we’ll use the levers at our disposal to partner and help organizations - and their customers. My executive team is available to discuss how Specright can help you navigate through this time.
Preparing for the Next Supply Chain Disruption
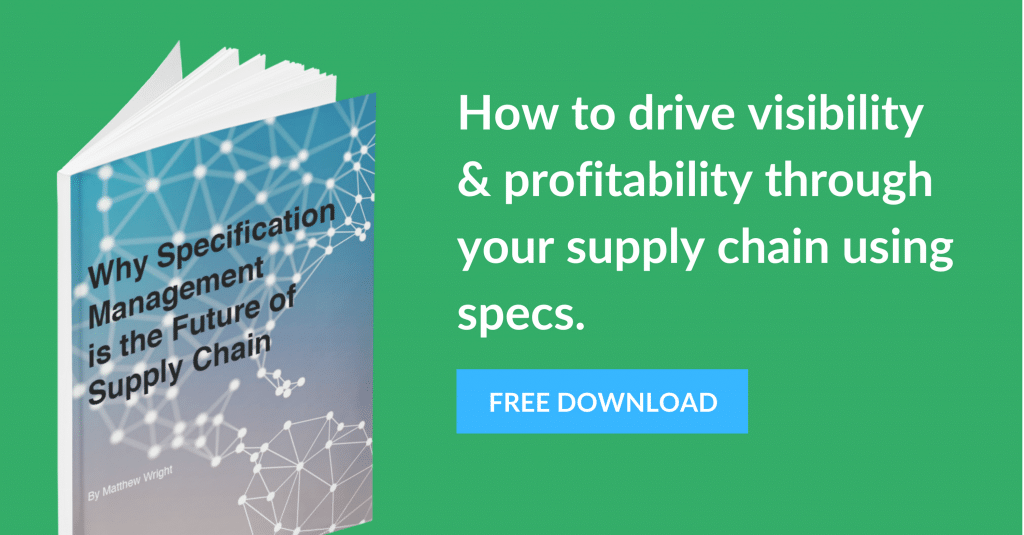
While I am confident that we as a society will get through this, the reality is manufacturing companies will need to be prepared for the next “coronavirus”-like event as supply chains have become increasingly complex.
I, along with my executive team, made the decision last week to transition our company to a “work from home” model. As a software organization, it was a simple transition. Since we work using cloud-based systems, as long as employees have their laptops and an internet connection there is no change in our capabilities or response times when it comes to serving our customers. It should be easier for manufacturers to do the same.
After all, as a society we can’t afford to have manufacturers making critical goods lose a step. It will take all of us making a small difference to make it through.